The surprising role of rainscreen cladding in 2025 growth
2024 was a challenging year for the building industry, with the UK construction sector experiencing a 22% decline in new orders during the third quarter of 2024; the lowest level since late 2023 (Office for National Statistics).
In addition to this, the industry is contending with a critical skills gap, with an estimated need for 350,000 additional construction workers over the next five years to meet decarbonisation goals (Reuters). Growing pressure from new regulatory changes such as The Building Safety Act 2022, as well as increases in material costs, and supply chain disruptions have added to the strain, putting financial pressure on construction firms across the UK.
Despite these challenges, the market is expected to return to steady growth from 2025 onwards, and we have recently seen news that the economy has grown in January for the first time in two months.
Interestingly, rainscreen cladding façade systems and the drive towards increased fire safety will play an important role in these changes; an impact that should be considered by architects, designers and contractors alike.
In this article, we explore how advances in sustainability requirements and technology, along with economic factors are collectively shaping the future of building design and construction.
Sustainability and energy efficiency:
Firstly, we cannot ignore the heightened focus on sustainable construction practices. Rainscreen cladding systems have been instrumental in improving building envelope performance, contributing to energy conservation and reducing carbon footprints.
The fundamentals of incorporating an air gap in rainscreen cladding, for example, creates a buffer between external and internal environments, improving thermal performance and reducing reliance on heating and cooling systems. Rainscreen cladding façades also offer superior protection against moisture infiltration, preventing water from penetrating the building envelope and causing damage to structural components, insulation, and finishes. By effectively managing moisture, rainscreen cladding can mitigate the risk of mould growth, rot, and deterioration, prolonging the lifespan of the building.
New technologies:
The adoption of advanced technologies has revolutionised rainscreen cladding systems and the development of large-scale buildings as a whole. Thanks to advanced techniques such as 3D modelling and printing, architects can now create highly complex and customised façade geometries, exploring novel forms, patterns, and textures in rainscreen façade design at minimal cost and with minimal risk.
A prime example of this is the £30 million pound Anglia Ruskin University (ARU) in Peterborough, which saw Optima TFC+ and Optima FC+ 3.0mm used to create the unique look and finish of the building.
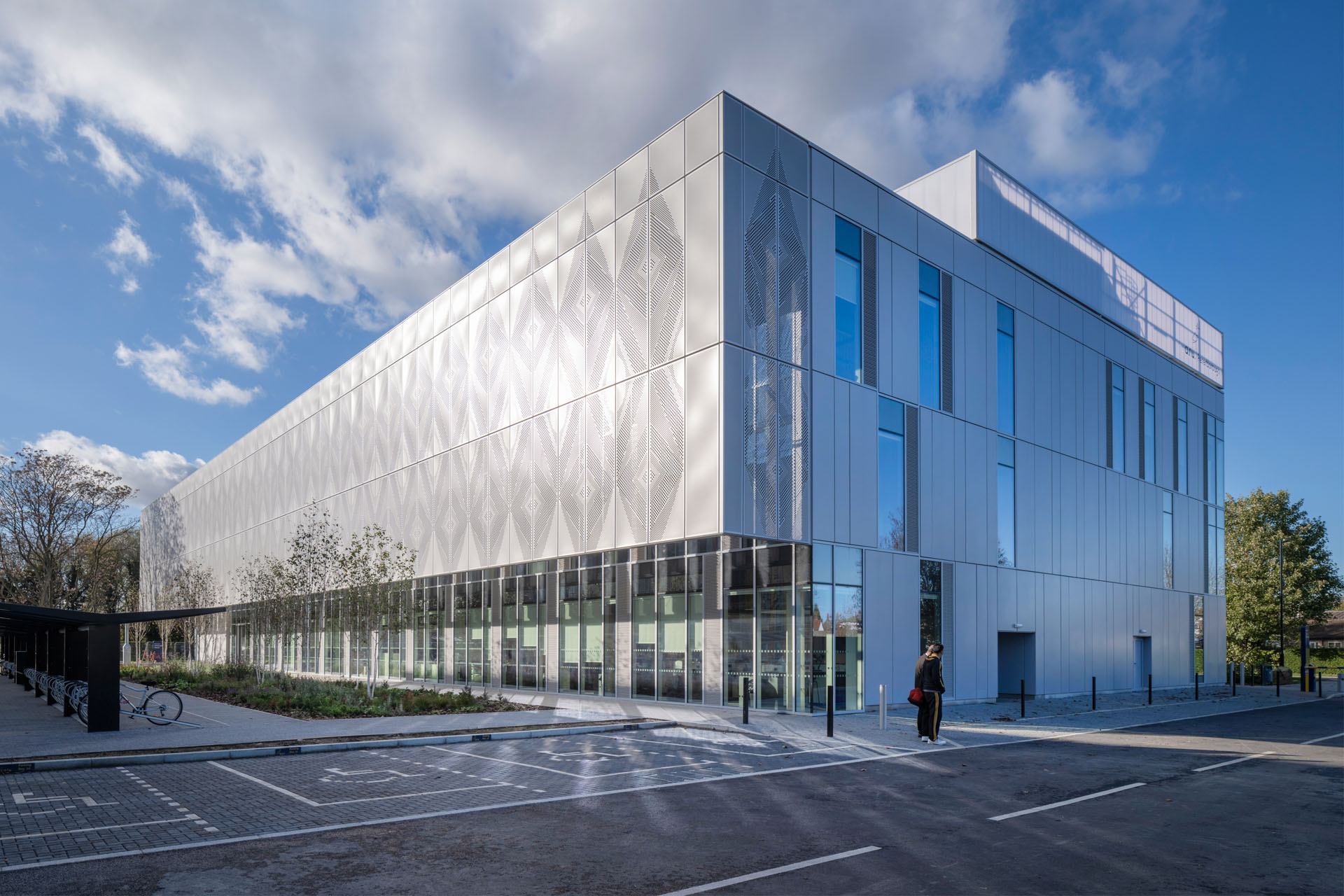
In this project, Sotech used advanced engineering simulation software to determine the thickness and alloy grade/temper for the perforated solar veil panels. The design team at Sotech worked their way from 3mm to 5mm in various grades to ensure best performance and best value for the project. The team also carried out extensive analysis using Finite Element Methodology (FEM) to determine that both stress and deflection in the panels are within permissible values, ensuring the most suitable alloy and optimal thickness for the project.
Another example can be seen in the brand-new Travelodge in Abbey Wood Retail Park, which used Optima TFC+ and Optima IPC.
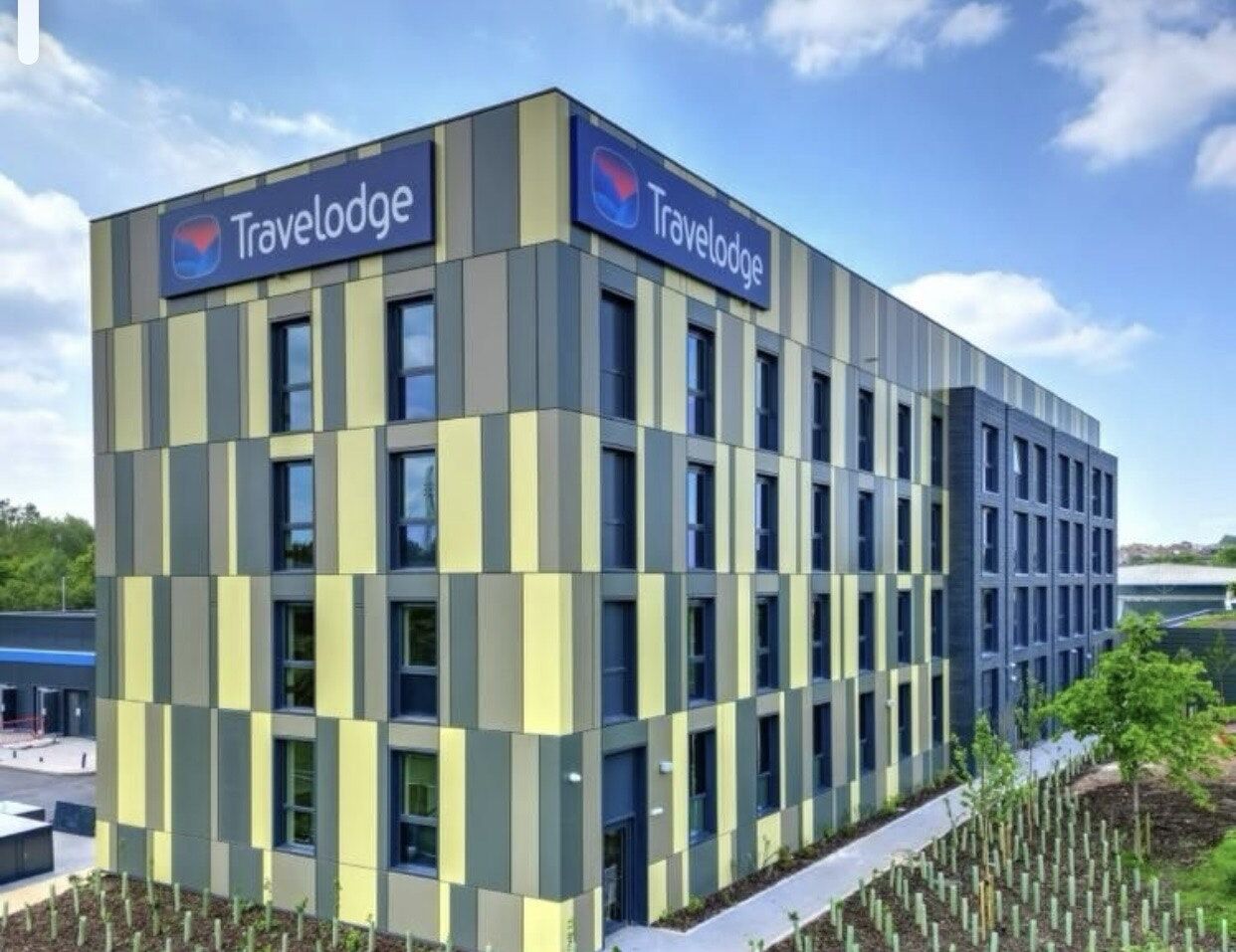
3D modelling was used from the beginning with the architect using Sotech BIM Objects to show how the panels, which don’t directly align in this example, would fit together in order to create bespoke order sheets for A2O to complete.
Using technologies like these increases speed in the design process, encourages innovation, and allows for testing long before full scale panels are produced.
Aesthetic inventiveness (and upgrades):
Finally, we have seen a huge amount of aesthetic inventiveness. Architects and designers have increasingly utilised rainscreen cladding to achieve diverse aesthetic outcomes. The flexibility in material choices and design possibilities has allowed for the creation of visually striking facades that align with contemporary architectural trends.
If we take a look at Discovery Quay in Salford, for example, we see a traditional cladding system being used creatively to produce the distinctive ‘basket weave’ pattern to the façade, which includes a mixture of both landscape and portrait orientation.
Building on phase 1 of the project, Sotech worked closely with Britplas Facades and their team of specialists to design the original façade, developing a method to secret fix the triangular sections onto standard panels at our fabrication facility. This reduced the quantity of parts the installer would have to handle but created a truly unique and inventive finish to the façade.
What’s interesting here is that older buildings are increasingly employing rainscreen cladding in full building reclads to both modernise their appearance and meet changing building requirements.
As an example, 3,500/m2 of Aluminium J57S Grade Anodised in United Anodisers Regency Gold 3 was used in the reclad of Glasgow’s Queen Street Station, for example, as part of a larger scale regeneration project for the station.
For the ICOSS building in Sheffield, Sotech provided Optima TFC+ in 3mm Aluminium as part of a recladding project to meet updated building requirements. The previous cladding was removed, and new, non-combustible anodised aluminium panels were installed.
Predictions for 2025
Market growth:
Whilst the global rainscreen cladding market is projected to experience substantial growth, with estimates suggesting that the global market size will reach approximately $21.67 billion by 2028, growth is expected to return more steadily in UK markets from 2025 onwards.
This growth is driven by increasing construction activities, particularly in the housing market, with a significant focus on energy-efficient building solutions and stringent fire safety regulations.
Current fire safety regulations in the UK, including the Building Regulations (Approved Document B), mandate that materials used in external wall systems for high-rise buildings over 18 metres must be non-combustible. This is typically achieved with materials rated A1 or A2-s1,d0 under the European Fire Classification system (Euroclass). By recladding a building in rainscreen cladding with the relevant fire safety classifications, buildings look better, and meet key safety requirements.
These factors are anticipated to boost demand for rainscreen cladding systems across various building projects, as A1 and A2 rainscreen systems provide tested fire-safe façade solutions that are functional, long-lasting and aesthetically pleasing.
This is vitally important in relation to The Building Safety Act 2022 (BSA) as increased scrutiny is driving the adoption of non-combustible insulation and cladding materials, regardless of building height, to comply with stricter fire safety requirements. Mineral wool insulation, for example, is gaining popularity due to its non-combustible properties and ease of installation. Not only is mineral wool highly compatible with the Optima range of rainscreen cladding systems, but it helps ensure compliance with the new regulations.
The UK market specifically benefits from trends like retrofitting of older buildings to meet updated safety and environmental standards. Projects like the Kings Buildings on the Edinburgh University campus, for example, were reclad in Optima TFC+ to provide an A1 rated finish.
Sotech is proud to provide full A1 rated rainscreen cladding systems, which employ non-adhesive fixing methods available for a true A1 and A2 rated cladding build up. Recladding older buildings in this way provides an effective way to bring buildings up to the current fire safety standards required in the UK, as mentioned above.
2025 Trends in Rainscreen cladding:
Based on specifications from the final quarter of 2024, here is what Sotech expects to see in 2025.
Advancements in materials:
Ongoing research and development are likely to yield new materials that offer enhanced durability, fire resistance, and environmental benefits.
In 2024, Sotech introduced an innovative variation on Optima FC+ to produce the fully integrated ‘living wall’ system. In early 2025, Sotech is set to announce a brand new product to market: Optima BrickTech – an alternative to traditional brickwork and cladding systems.
This new solution seamlessly combines the classic aesthetics of real, natural bricks with the advanced performance of modern cladding technology. Engineered for durability and ease of installation, the Optima BrickTech system is designed to work with a range of brick types, redefining brickwork in contemporary architecture with a visually appealing facade and superior functionality, offering a superior approach to traditional brick cladding with a range of benefits that enhance the functionality and aesthetic of buildings.
The introduction of innovative cladding materials, like this, will provide architects and builders with more options to meet both regulatory requirements and design aspirations.
For example, BrickTech has been independently tested – Certified to CWCT Sequence B – and uses anodised aluminium profiles (6063T6) that comply with BS EN 755-9:2016, ensuring high-quality and certified materials.
Likewise, Sotech has seen a huge growth in demand for anodised aluminium rainscreen products. Anodising is an A1 non-combustible finish that increases the thickness of the natural oxide layer on the surface of metal parts. Colours, textures and patterns can also be incorporated in the anodic film, enhancing the natural metallic appearance without affecting the total UV resistance of the rainscreen cladding.
A brand new leisure centre in Hartlepool in the North East is using anodised aluminium for these exact reasons, with the new ‘active welling hub’ now well underway. Designed by GT3 Architects, the building will feature strong linear lines, inspired by the railway tracks which ran from local timber and coal yards into the former dockland site during the 19th and early 20th centuries.
This perfectly demonstrates the power of rainscreen cladding, which not only provides a safe and long-lasting exterior façade, but can also be used to bring a local story to life.
Regulatory changes:
Governments are expected to implement stricter building codes focusing on energy efficiency and safety. Not only is The Building Safety Act driving significant changes in the selection, design, and implementation of rainscreen cladding systems, but the UK government is considering further reforms recommended by the final Grenfell Inquiry report, which may lead to additional changes in building regulations and guidance.
Rainscreen cladding systems will need to comply with these evolving standards, prompting manufacturers to innovate and adapt their products accordingly. The BSA, for example, has established a more stringent regulatory framework, particularly for higher-risk buildings. Sotech is proud to have been so proactive in addressing these requirements, with the Optima range of rainscreen cladding solutions providing A1 and A2 fire-rated systems (with non-combustible fixings) long before it became law.
Adding to this, developers are now required to obtain building control approval from the Building Safety Regulator before commencing work, ensuring that building designs meet enhanced safety standards. This increased scrutiny is expected to drive the adoption of non-combustible materials in rainscreen cladding systems to comply with stricter fire safety requirement.
Beyond safety requirements like this, we are also seeing a drive towards ‘biodiversity net gain’ through the Environment Act 2021, which requires developers to enhance urban environments and bring back wildlife to our densely populated cities. This new obligation became effective from February 2024 and requires developers to achieve a BNG of 10%, meaning that the development must result in a net increase in the quantity or quality of natural habitats.
Speaking at the 2024 Data Centre Dynamics (DCD) Connect event in London, our very own Graham Todd (Director at Sotech), and supply partner Alistair Law Founder of Vertical Meadow, spoke about the transformative potential of living rainscreen and vertical greening solution as a unique solution to enhancing urban biodiversity.
Using Data Centres as an example, Alistair made a case for structures like this being assets to cities as they transform conventional buildings into thriving ecosystems that not only meet technological needs but also contribute positively to local communities, with practical benefits improved air quality, reduced urban heat island effect, and enhanced building aesthetics in busy areas.
Labour market dynamics:
The UK construction industry is currently facing a significant shortage of skilled labour, a challenge that has been impacted by factors such as Brexit, the COVID-19 pandemic, and an aging workforce. This shortage has led to increased labour costs, with projections indicating an 8.3% rise in 2023, and has extended project lead times by up to 50%, forcing contractors to re-scope projects.
To mitigate these challenges, the industry is increasingly turning to modern methods of construction (MMC), particularly modular construction. Modular construction involves the off-site fabrication of building components in controlled factory settings, which are then transported to the construction site for assembly.
In the development of Ferry Lane in London, for example, the ‘plank’ and ‘wave’ profiles of Sotech’s Optima XTR were manufactured off-site and then installed on-site, to save time during the installation phase.
Likewise, Kelaty House in Wembley saw Sotech’s Optima FC+ system with perforated aluminium panels manufactured off-site, anodised by a partner company, and then delivered to the site for installation. This process ensured high precision and quality while reducing on-site construction time.
Beyond this, digital fabrication technologies such as CNC milling, laser cutting, and robotic manufacturing enable the precise fabrication of façade components with less reliance in skilled personnel to do the job.
Sotech’s manufacturing facilities incorporate some of the very latest and most technologically advanced machinery, including a number of CNC pressbrakes (folding millimetre perfect parts up to 6M long, which is larger than the current industry standard), a rapid automated punching machine (producing bespoke shapes and perforated blanks to a high tolerance), a 12M CNC router (cutting composite, solid material blanks and intricate shapes with a smooth finish), along with a fully automated production line that turns flat metal sheets into finished panels in seconds.
Despite this, businesses still run on people and the recruitment and training of new starters on apprenticeships has been equally important to the sustainable growth of Sotech. Since 1984, Sotech has actively integrated apprentices into its workforce, with over half of the current team having begun their careers as apprentices. Sotech believes in nurturing talent at every stage, which is why the company offers apprenticeship opportunities across different levels and ages within the business. From school leavers to career development, apprentices at Sotech gain hands-on experience and expert training to continue the development of real talent in house.
In conclusion:
The trends of 2024 have set the stage for a dynamic and evolving construction landscape in 2025. Rainscreen cladding systems are at the forefront of this transformation, addressing key challenges such as fire safety, sustainability, and modern construction methods while delivering exceptional aesthetic and functional results.
At Sotech, we are proud to lead this transformation with innovative solutions like Optima Edge , Optima Meadow and Optima BrickTech, designed to meet the evolving demands of architects, designers, and contractors. As the industry moves forward, collaboration, adaptability, and forward-thinking will be key to driving efficiency and growth.
With over 40 years of experience, Sotech has been at the forefront of developing non-combustible, fire-safe products rigorously tested to the highest standards. Our Optima range includes true A1 and A2-rated materials such as PPC Aluminium, Anodised Aluminium, Pre-Painted Aluminium, Corten Steel, Stainless Steel, and Zinc, offering a variety of finishes to meet both aesthetic and performance requirements while ensuring compliance with the latest fire safety regulations.
Contact us today to learn more about our cutting-edge products and how we can support your next project.